The consortium is very confident with the IBMC production process and very optimistic with the project evolutio
VIPRISCAR, the European project focused on the development and validation of a highly-efficient isosorbide bis-methyl carbonate (IBMC) production process as a renewable raw material, has overcome its midpoint. The project will demonstrate the usefulness of IBMC in the synthesis of polymers for industrial coatings, adhesives, and medical devices.
A project meeting has taken place in the new Technology Center at JOWAT headquarters (Detmold, Germany). During this meeting, the project partners have analyzed the obtained results, have shared their impressions about the developed advances during these first 20 months, and have reevaluated the objectives of the project. The consortium has demonstrated its confidence in the executed work and it is very optimistic about the project evolution. At this moment, more than half of the objectives established at the beginning of the VIPRISCAR project have been successfully achieved, promising very good expectations about the exploitation of the results of the project.
The consortium has demonstrated its confidence in the executed work and it is very optimistic about the project evolution. At this moment, more than half of the objectives established at the beginning of the VIPRISCAR project have been successfully achieved, promising very good expectations about the exploitation of the results of the project.
The work performed within the VIPRISCAR project during this first period has been focused on moving the IBMC production process from initial proof of concept (TRL 3) to a validation stage in both laboratory (TRL 4) and in a relevant industrial environment (TRL 5). For this purpose, a robust process that combines reaction and purification processes has been developed to obtain different IBMC purities, up to 99 wt%. It can deal with different raw material (isosorbide) grades commercially available which are characterized by their different content in acidic impurities.
For this purpose, a robust process that combines reaction and purification processes has been developed to obtain different IBMC purities, up to 99 wt%. It can deal with different raw material (isosorbide) grades commercially available which are characterized by their different content in acidic impurities.
This process has been monitored to obtain the corresponding simulation models that permit to establish the basis of a further scale-up. In this sense, a pilot unit of 200L is already constructed and successfully commissioned to produce the first IBMC batches. Using this pilot unit, 100 Kg of IBMC will be produced by the end of May 2020.
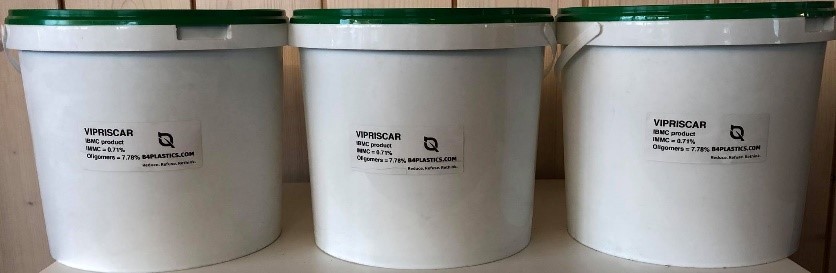
Activities focused on the production of polymers from IBMC have also started. The initial IBMC based oligocarbonates, polycarbonate polyols and NIPUs dispersions have already been obtained. The optimized pre-polymers will be used for coatings in the automotive and furniture sectors, hot-melt adhesives and catheters for biomedical applications. Industrial applications are closer and closer. The exploitation possibilities for IBMC are clearer and clearer.